Gedruckte Einwegelektronik kompostieren
Biomüll statt Elektroschrott: Für biologisch leicht abbaubare elektronische Bauteile entwickelt die BMBF-Nachwuchsgruppe Biolicht am KIT nachhaltige Druckmaterialien und Tinten.
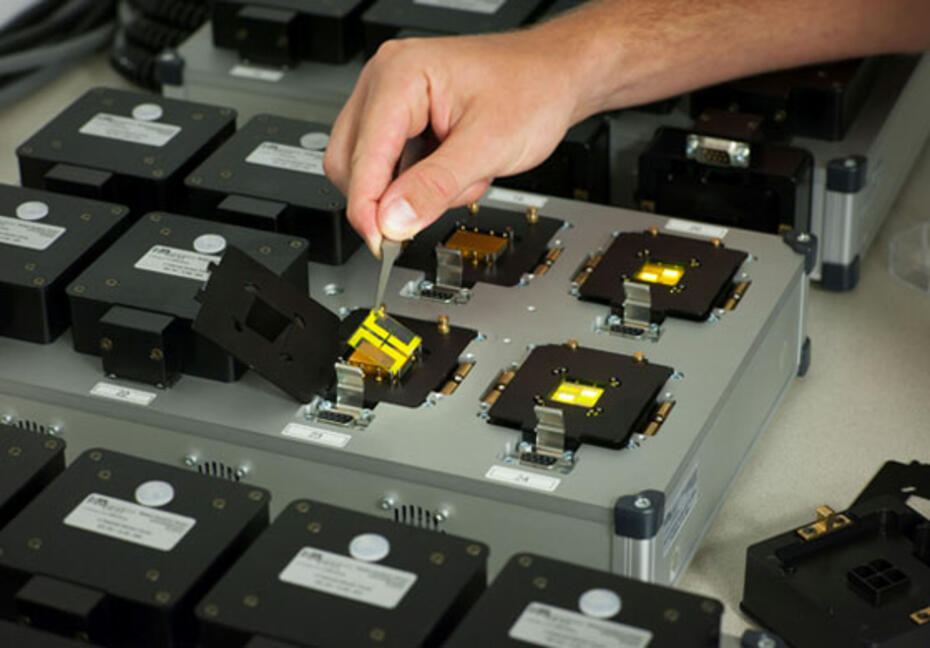
Knapp zwei Millionen Tonnen Elektroschrott fallen pro Jahr in Deutschland an. Gedruckte Elektronik befördert den Wegwerftrend, indem sie Herstellungskosten senkt und mit Einwegprodukten, wie interaktiven Verpackungen oder intelligenten Pflastern, neue Märkte erschließt. Nachwuchsforscher am Karlsruher Institut für Technologie (KIT) entwickeln daher gedruckte Elektronik aus kompostierbaren Naturmaterialen sowie Verfahren für eine industrielle Produktion.
Halbleiter und Farbstoffe aus Pflanzenextrakten oder Isolatoren aus Gelatine – die Nachwuchswissenschaftler arbeiten mit biologisch leicht abbaubaren Materialien. »Diese sind zwar nicht so langlebig wie die anorganischen Alternativen, doch die Lebensdauer von Einwegelektronik überstehen sie schadlos«, sagt Dr. Gerado Hernandez-Sosa, Leiter der nun eingerichteten Nachwuchsforschergruppe ›Biolicht‹. Zudem könne man die Elektronik, sobald sie ausgedient hat, einfach in den Biomüll oder auf den Kompost werfen, wo sie gleich einer Bananenschale verrottet.
Geduckte Elektronik besser recyclen
Für gängige gedruckte Elektronik, etwa für organische Leuchtdioden (OLEDs), gilt dies bislang nicht. »Als ›organisch‹ bezeichnen wir alle Kunststoffe auf Kohlenstoffbasis. Über die Umweltverträglichkeit sagt der Begriff allein noch nicht aus«, erklärt Dr. Hernandez-Sosa. So sei beispielsweise die Trägerfolie von OLEDs – das Papieräquivalent für elektronische Tinten – aus dem gleichen Plastik wie herkömmliche Getränkeflaschen. Die Nachwuchsgruppe Biolicht verwendet hierfür nur Materialien, die in der Natur tatsächlich vorkommen.
Als Trägerfolien eignen sich beispielsweise Speisestärke, Zellulose oder Chitin. Auf Metalle und Halbmetalle, wie Silizium, verzichten die Wissenschaftler fast vollständig. Der Vorteil von Plastik: Es ist biegsam, kostengünstig und lässt sich zu kilometerlangen Druckerfolien verarbeiten. Mit dieser Technologie wird es möglich, etwa Aufkleber mit einer elektronischen Ampel für das Haltbarkeitsdatum oder Pflaster mit eingebauten Sensoren, die den Heilungsprozess überwachen, im industriellen Maßstab herzustellen.
Zunächst gilt es allerdings auf die kompostierbaren Folien elektronische Bauteile zu drucken, ähnlich wie Buchstaben auf Papier. Ihre Funktion hängt von der verwendeten Tinte ab: Anstelle von Farbpartikeln sind darin leitende, halbleitende oder isolierende Materialien gelöst. Nach dem Auftragen trocknet das flüssige Lösemittel und die zurückbleibende Schicht bildet das entsprechende Bauteil.
Ziel der Nachwuchsgruppe ist es, biologisch abbaubare Tinten zu entwickeln, die auf das neue Folienmaterial abgestimmt sind und gleichzeitig mit bestehenden Geräten gedruckt werden können. »Hersteller organischer Elektronik können so auf die um-weltfreundlichen Materialien umsteigen, ohne ihr Druckerarsenal auszutauschen«, sagt Dr. Hernandez-Sosa.
Für die Tinten müssen die Nachwuchswissenschaftler nun umweltverträgliche Materialien mit den gewünschten elektrischen Eigenschaften identifizieren. Beispielsweise eignet sich Hartgelatine, aus der Medikamentenkapseln bestehen, zum Isolieren. Aufwendig ist auch die Wahl des Lösemittels: Eine Voraussetzung ist, dass es bei druckfähigen Temperaturen in flüssiger Form vorliegt. Weiterhin darf es im Unterschied zu gewöhnlicher Tinte nicht in das Trägermaterial eindringen, sondern sollte darauf einen geschlossenen Flüssigkeitsfilm bilden, ohne abzuperlen. Ein zu dickflüssiges Lösemittel verstopft die Poren des Druckers. Ein zu dünnflüssiges verläuft auf der Trägerfolie und benetzt sie nicht gleichmäßig. Die Eigenschaften des getrockneten Materialfilms sind aber für die Funktion der elektrischen Bauteile entscheidend: So darf seine Dicke, die weniger als einem tausendstel Millimeter beträgt, maximal um fünf Prozent schwanken. Die Wissenschaftler rechnen damit, kompostierbare organische Elektronik innerhalb der nächsten drei Jahre marktreif zu machen.
Die Nachwuchsgruppe Biolicht ist strukturell am Institut für Lichttechnik des KIT angesiedelt. Ihre Labore hat sie am InnovationLab in Heidelberg. Träger sind neben dem Karlsruher Institut für Technologie, die Unternehmen BASF, Merck, Heidelberger Druckmaschinen und SAP sowie die Universität Heidelberg. Das Bundesministerium für Bildung und Forschung unterstützt die Nachwuchsgruppe für vier Jahre mit insgesamt 1,7 Millionen Euro.